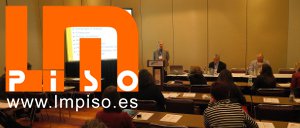 |
John McGrath, director of the International Standards & Training Alliance (INSTALL), led the Flooring Disaster: Prevention and Recovery seminar at IIDEXCanada in Toronto. |
John McGrath, director of the International Standards & Training Alliance (INSTALL), led the Flooring Disaster: Prevention and Recovery seminar and panel discussion at Toronto’s IIDEXCanada design and architecture expo and conference.
According to McGrath, flooring contractors can’t be scapegoats, every time a floor fails and due diligence has to start higher up the contractor chain. "General contractors and other subcontractors must understand that some of their activities can cause substrate problems for flooring installers, ranging from improperly leveled concrete floors to moisture intrusion in the slab. It is the best insurance policy to protect everyone involved."
Panelist Steve Zizek, flooring instructor, Resilient Floor Workers Training Trust Fund, Carpenters Local 27, added, "The cause of flooring problems is often related to the condition of the substrate. And it can be in poor shape long before the flooring contractor’s arrival on site."
Panelist Dave Furlano, owner of Centa Tile added, “Flooring contractors are one of the last trades on site—oft-times facing a tight schedule and a substrate that sometimes is ill-prepared for flooring. Often we’ve got issues of oil spillage on floors (typically oil from hydraulic lifts on site) and we’re told it is our problem. Oil stains are nearly impossible to clean and today's flooring contains latex adhesives which won’t adhere to petroleum products."
The solution, according to Zizek is sometimes the concrete slab has to be ground down and topped with a self-leveling concrete. It can be “an added huge cost” that no flooring installer could see coming at the tendering stage. Furlano said by getting involved early in the pre-construction process, flooring contractors can play an important role in mishap prevention. Hydraulic lifts, for example, can be equipped when operating on the slab with oil catching “diapers” to prevent spillage. He advised flooring contractors to visit the site occasionally—even if they aren’t scheduled to start the job for months—to review conditions, including floor level and finish.
While moisture in the substrate is a major problem, moisture measurement tests can be performed well in advance of the flooring installer’s arrival. Those tests should be the general contractor’s responsibility, but they are often written into the flooring contractor’s specs, said Zizek.
Furlano said even when his firm performs moisture tests, for relative humidity and calcium chloride, for example, the installation can still be in danger if the vapor retarder is incorrectly used. Moisture can continue to leach up from beneath the slab—particularly on wet or swampy sites.
Zizek added while moisture remains a major culprit for flooring failures, today’s high-quality moisture mitigation products provide improved protection from moisture failure. In Furlano’s contracting experience, one of the leading causes of flooring failure is maintenance crews that don’t familiarize themselves with the appropriate cleaning products and methods.
"Maintenance comes under the product warranty and all leading manufacturers have detailed information on proper maintenance," said McGrath.
For more information, visit .